- Rolling Body:Ball Bearings
- The Number of Rows:Double
- Outer Dimension:Large (200-430mm)
- Material:Alloy
- Spherical:Aligning Bearings
- Load Direction:Radial Bearing
=== Base Info ===
- Model NO.:FDSP
- Separated:Separated
- Brand:Fdsp
- Name:Roller Shell_Pellet Mill Roller Shells for Sale
- Application:for Ring Die Pellet Mill
- Customized:Cpm,Muyang, Bulher
- Transport Package:Iron Case
- Specification:CE, ISO, SGS
- Trademark:Liangyou
- Origin:Jiangsu China
- HS Code:8436100000
- Production Capacity:400-500h
=== Description ===
Basic Info.
Model NO.
FDSP
Separated
Separated
Brand
Fdsp
Name
Roller Shell_Pellet Mill Roller Shells for Sale
Application
for Ring Die Pellet Mill
Customized
Cpm,Muyang, Bulher
Transport Package
Iron Case
Specification
CE, ISO, SGS
Trademark
Liangyou
Origin
Jiangsu China
HS Code
8436100000
Production Capacity
400-500h
Product Description
Roller Shell for Ring Die Pellet Mill Alloy Steel HRCType | honey-comb type, teeth or customized |
Application | spare parts for pellet mill, like feed pellet mill, bio-mass pellet mill |
| Our roller shell is for pellet mill from CPM, BULHER, MUYANG, ETC |
Feature of FDSP roller shell
1Roller shell,made of wear resistant alloy raw material, processed by fine and heat treatment;
2Made of bearing steel, high hardness, good wearing resistance, long life, different tooth depth and shape at option;
3 Tooth surface forms of roller shell, good to pelleting performance
4 Frequently-used roller shell tooth form:honeycomb,scallop shape and scallop shape with edge banding
5 Honeycomb,scallop shape, the two types of roller shell is mainly used in livestock and poultry feed pelleting.
6 The advantage of honeycomb rolller shell is the even wearing of ring die, but coil performance is bad.
7Scallop-shaped roller shell features good coil performance, widely used among feed mills, but wearing of ring die is not even.
8Scallop shape with edge banding, this kind of roller shell is applicable for aqua feed. Feed is not easy to slide towards both sides when being extruded.
Plenty of pellet mill parts are in stock.
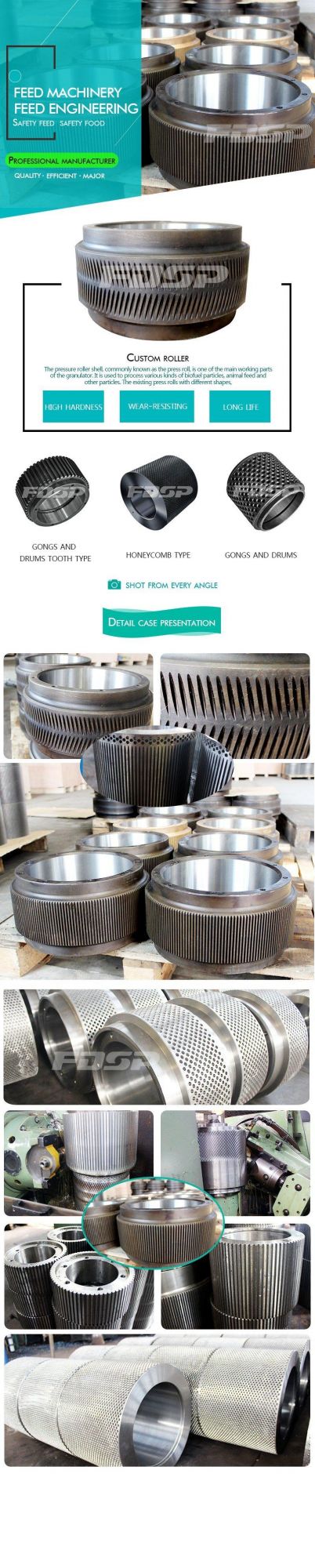
Product Description:
Roller shell, commonly known as roller, is one of the main work parts in pellet mill and is applied for processing various kinds of biomass fuel granule, animal feed pellet and other pellets. It is made of wear resistant alloy steel with carburization heat treatment, featuring even hardness and long service life. It is divided into tooth through type, tooth no through type and pass type. Rolling parts such as inner eccentric shaft are precise in size, facilitating space adjustment by customers between roller and ring die according to production requirement. It is also characterized by ease of mounting and replacing.
Notice:
1.Select correctly appropriate die hole compression ratio
2.Correctly adjust the working clearance between ring die and roller, from 0.1 to 0.3 suitable.(after new pellet mill being switched on, roller, driven by ring die, getting into a state of prerunning,but not rotating.)
3.New ring die should match new roller to use.Roller connecting with ring die must be loose in front and tight in back.When roller two sides appear sharp corners, it should be timely used hand grinder to blunt the flange part so as to have a good connection of roller and ring die.
4.Before raw material fed into pellet mill,precleaning and magnetic separation treatment is necessary in order to minimize iron impurities of getting into die hole.Checking regularly the die hole is also essential to see whether the die is blocked and accordingly clean the blocked die hole.
5. If plastic deformation happens to ring die guiding material cone hole,causing hole shrinking, it must be repaired.During repairing, pay attention to that ring die inner surface lowest height must be 2mm higher than the bottom of overtravel groove.In addition,the eccentric shaft adjusting must allows an extra, otherwise ring die should be scraped.