- After-sales Service:Spare Parts, Field Service
- Type:Starch Machine and Turnkey Plant
- Application:All
- Voltage:380V
- Press Materials:Corn
- Condition:New
=== Base Info ===
- Model NO.:maize milling plant
- Customized:Customized
- Brand:Myande
- Capacity:60000-600000t,a
- Raw Material:Maize
- Product:Starch ,Gluten
- After-Sales Service Provided:Engineers Available to Service Machinery Overseas
- Worker Quantity:3-5persons Per Shift with Auto-Control System
- Delivery Time:6 Months
- Installation Time:6 Months
- More Information:Design by Customer′s Requirements
- Transport Package:Container
- Specification:ISO
- Trademark:Myande
- Origin:Yangzhou, Jiangsu
- Production Capacity:200units,Year
=== Description ===
Basic Info.
Model NO.
maize milling plant
Customized
Customized
Brand
Myande
Capacity
60000-600000t/a
Raw Material
Maize
Product
Starch ,Gluten
After-Sales Service Provided
Engineers Available to Service Machinery Overseas
Worker Quantity
3-5persons Per Shift with Auto-Control System
Delivery Time
6 Months
Installation Time
6 Months
More Information
Design by Customer′s Requirements
Transport Package
Container
Specification
ISO
Trademark
Myande
Origin
Yangzhou, Jiangsu
Production Capacity
200units/Year
Product Description
Turnkey Maize Corn Starch Machine, Corn Wet Milling Factory Supplier1. Process DesignA) Corn Steeping Section
Corn Steeping Section generally adopts semi-continuous counter-current steeping process with 8-12 tanks. Steeping time would be last about 48 to 56 hours according to the contents of corn varieties, quality and moisture.
B) Corn Degerming Section
Corn Degerming section adopts two-stages DEGERMING MILL to break and two-stages cyclone to degerm.
C) Fine Mill and Fibre Separation Section
Fine Mill adopts PIN MILL to separate the starch from the fibre.
D) Starch Separation and Gluten Concentration Section
Myande Centrifugal Separator can be used in this section according to different capacities to separate the starch and gluten, also you can adopt the process method such as first preconcentration, then separation and later middle concentration. Also about the refined starch section, we use MULTI-STAGES WASHING CYCLONE. In gluten concentration section. CENTRIFUGAL SEPARATOR can be used according to different capacities. Usually, for gluten dewatering, we use VACUUM FILTER or frame type filter in the section.
E) Starch Dewatering and Drying Section
First, we use siphon type scrape centrifuge for dewatering and then use NEGATIVE PRESSURE FLASH DRYER to control the moisture of the final product automatically.
F) Corn Steeping Solution Evaporating Section
We would like to use fresh steam or waste heating as heating energy in the corn steeping solution evaporation section. Then make use of MULTI-EFFECT EVAPORATOR to evaporate. All these can be designed differently depends on the customers' requirement. The steeping solution after concentration can be offered for sale directly, if not, it also can be mixed into the fiber to be dried as fiber feed with protein.
G) Drying and Packing Section
In this section, usually, we take the TUBULAR BUNDLE DRYER to dewater the moisture in fiber, germ and protein powder.
2. Engineering CapabilitiesA) Providing complete corn starch processing equipment line with capacity ranging from 60,000 to 600,000 tons per year.
B) Complete engineering services from process and equipment design, fabrication, installation & commissioning, and after-sale technical support.
C) Meticulous 3D design creates a direct, accurate and clear presentation of every detail of the project design.
D) Advanced automatic control system ensures high reliability of the whole production line.
3. After-sales ServiceBefore sale, we can help the buyers in planning the general plan.
Generally, we guarantee all equipment are completely new and unused, and under normal operating conditions the warranty period would be 12 months after installation or 18 months from the date of shipments whichever comes first.
Our equipment would be shipped in containers. Equipment with too large size for containerized shipment would be covered and protected from seawater damage.
We can send experienced and qualified engineers (electrical engineer and mechanical engineer) to the Buyer's site for the supervision of equipment installation and commissioning. And after the plant had been successfully commissioned, our engineer will stay to train the buyer's plant personnel in process operations and equipment maintenance by buyer's request.
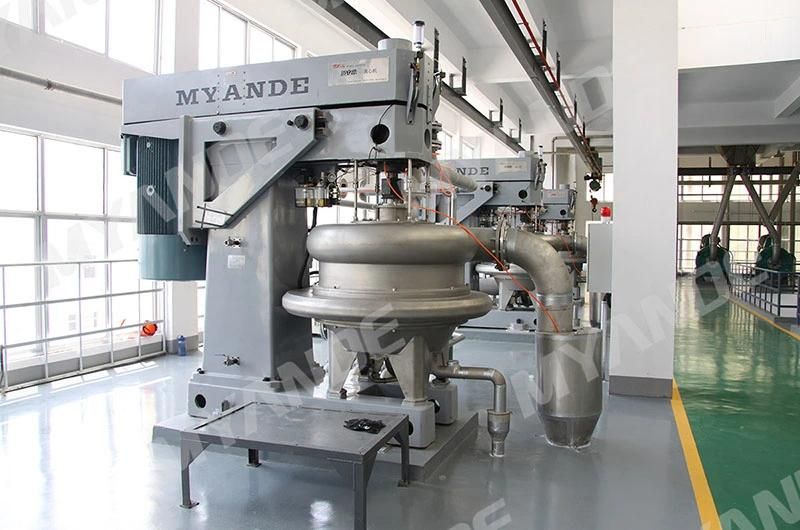
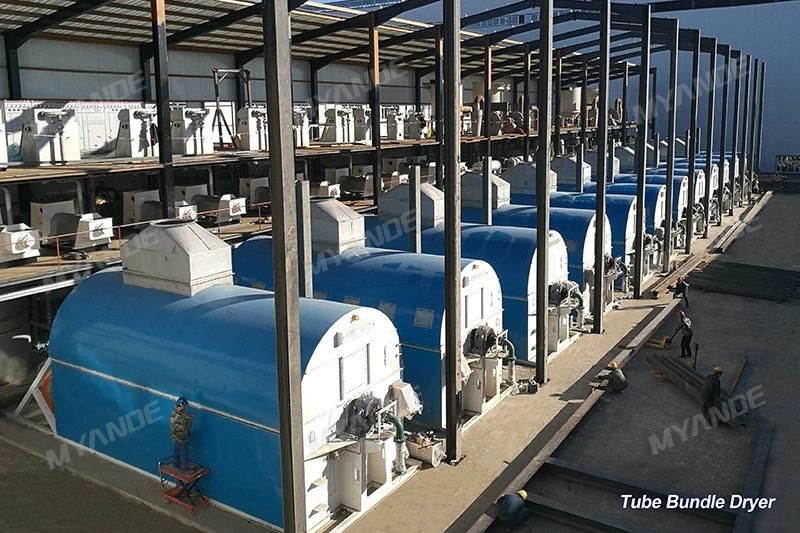
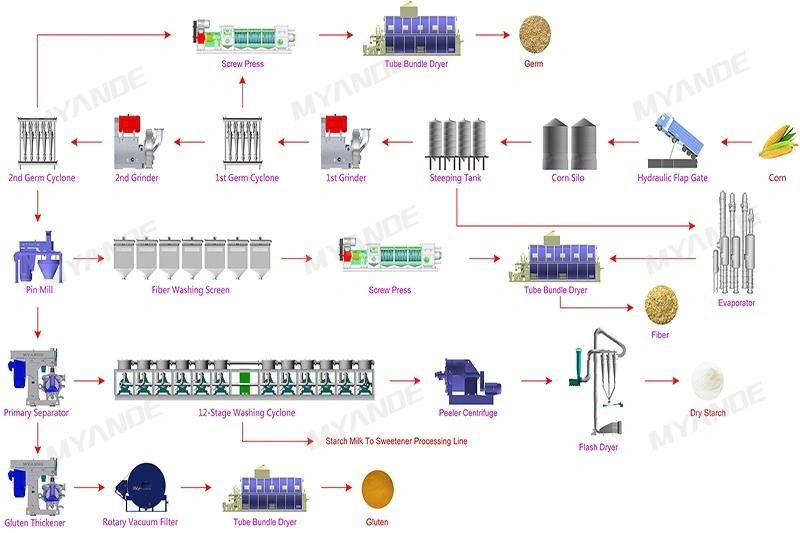
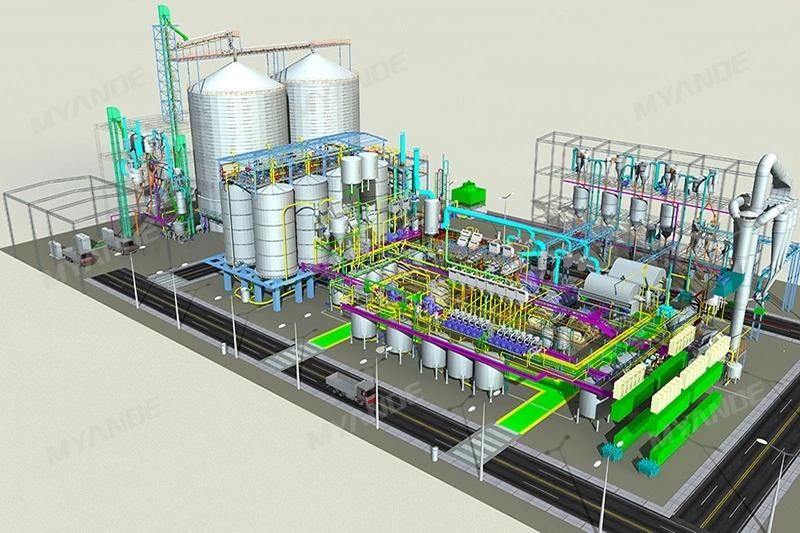
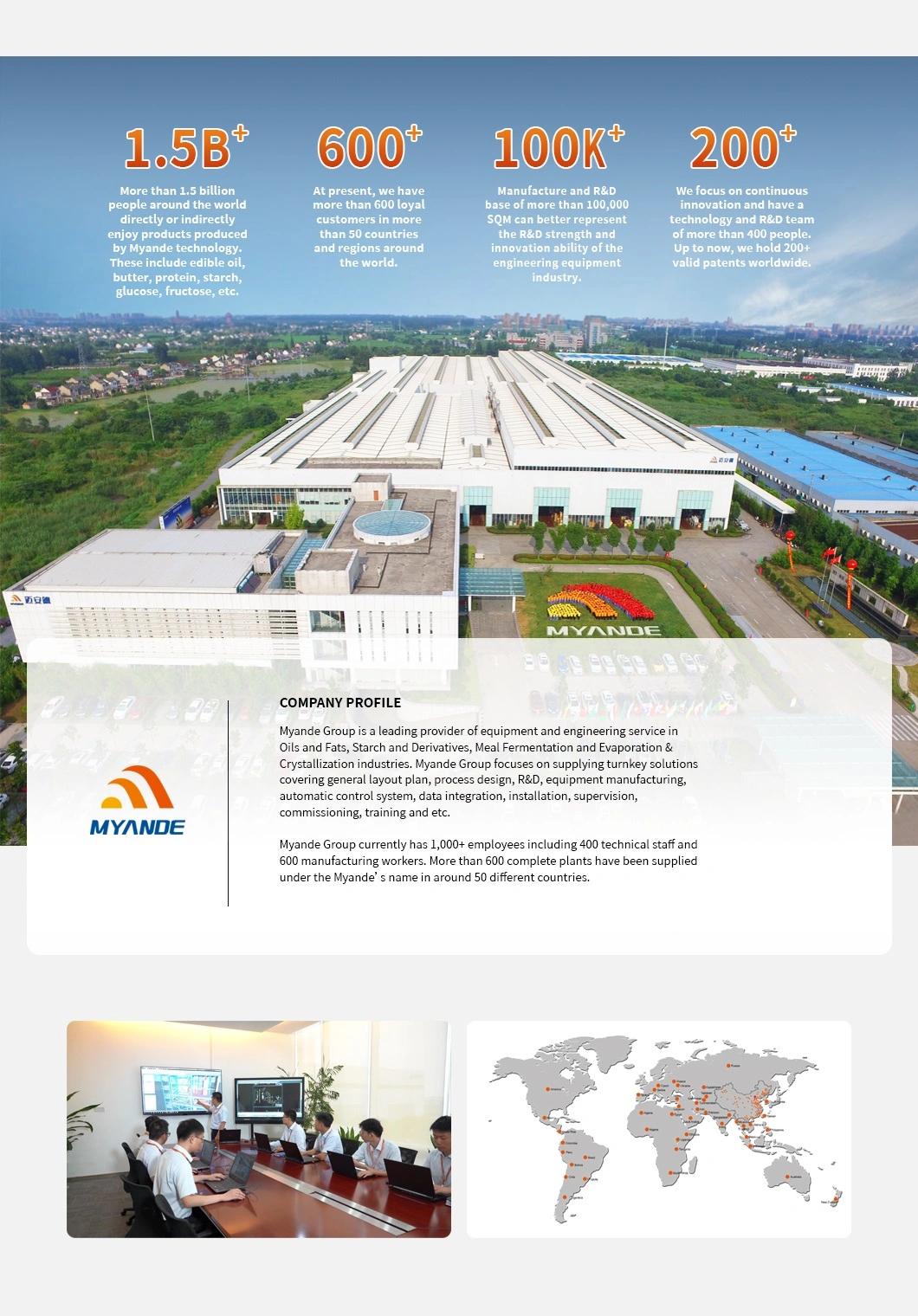
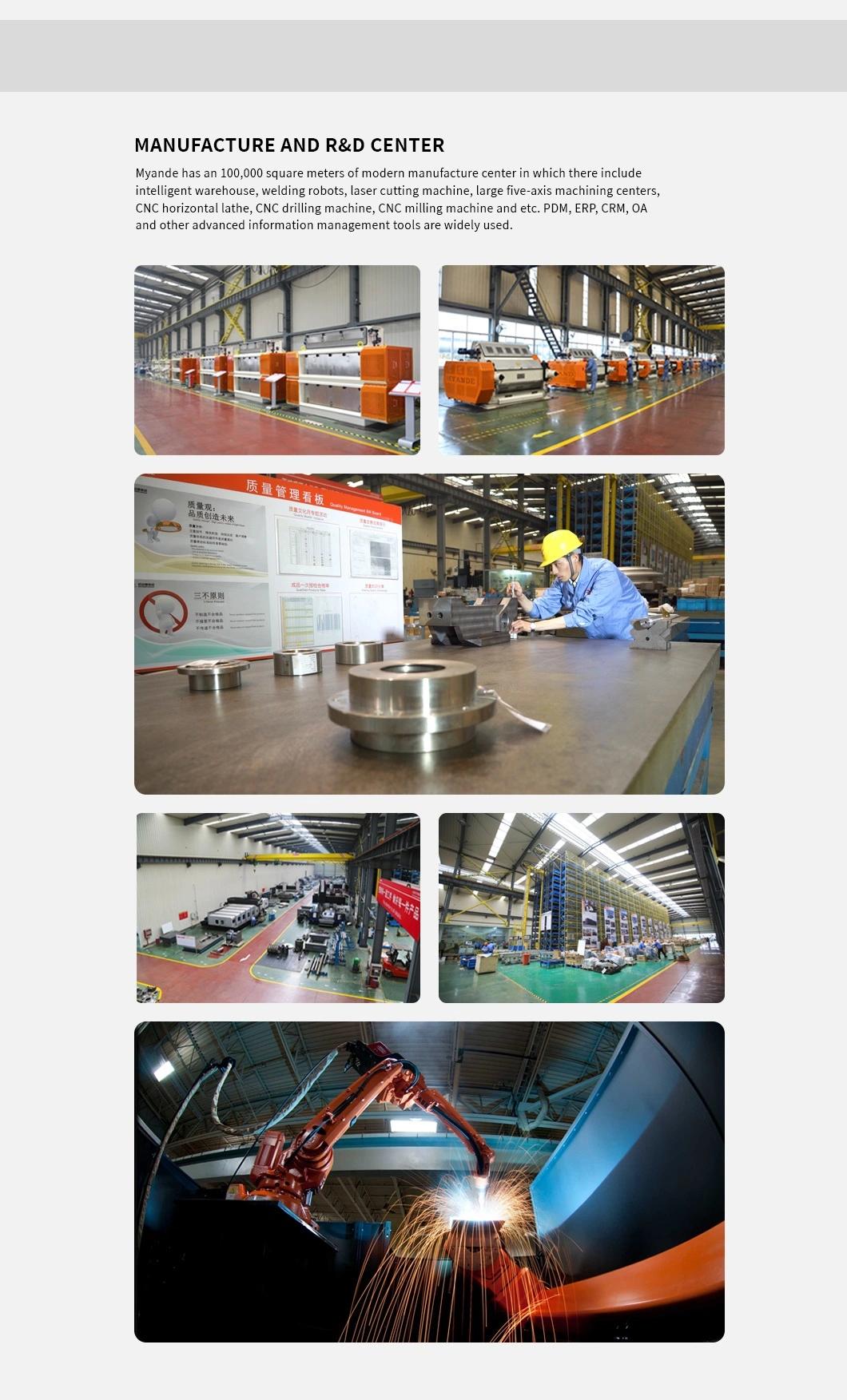