Cooking Oils Degumming Bleaching Deodorise Production Line
Shenzhen Xiangfeizhu Technology Co., Ltd. / 2022-07-05
- Type:Oil Refining Equipment
- Application:Edible Oil
- Voltage:220V
- Appearance:Vertical
- Press Materials:Soybean
- Press Series:Second
=== Base Info ===
- Model NO.:Huatai-Refining
- Condition:New
- Customized:Customized
- Capacity:10tpd-500tpd
- Section:Degumming, Bleaching Deodorization Dewaxing
- Transport Package:Bulk
- Specification:Customized
- Trademark:Huatai
- Origin:China
- HS Code:84792000
- Production Capacity:10 Sets Per Year
=== Description ===
Basic Info.
Model NO.
Huatai-Refining
Condition
New
Customized
Customized
Capacity
10tpd-500tpd
Section
Degumming, Bleaching Deodorization Dewaxing
Transport Package
Bulk
Specification
Customized
Trademark
Huatai
Origin
China
HS Code
84792000
Production Capacity
10 Sets Per Year
Product Description
Henan Huatai Cereals and Oils Machinery Our company was estabished in 1950s ,now is one of the big oil equipment supplier in China .We have our own R&D department and installation service team with rich experience . We have successfully obtained 27 national patents (7 invention patents), 6 international medals, 2 state awards, 2 provincial prizes Our machines sell well in more than 30 provinces, and exported to Egypt, Sudan, Tanzania, Rwanda,Nigeria,Estonia,Russia,Kazakhstan,Uzbekistan,Tajikistan,Bangladesh,Thailand,Malaysia,Indonesia, Bolivia,Peru and so on.Now we have developed into a major oil machinery manufacture base in China.
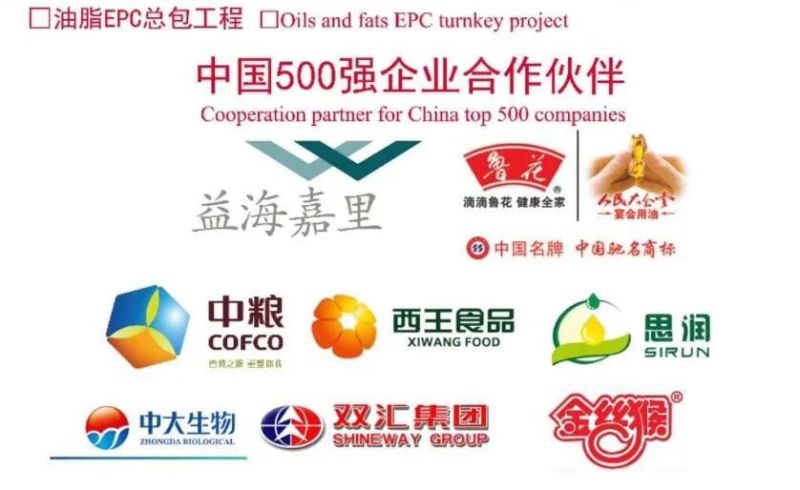
Oil Refining Process DescriptionPlant includes neutralization,bleaching, deodorization and vacuum auxiliary sections:--- Neutralization sectionCrude oil from tank area is sent to crude oil tank in the workshop by pump, after accurate measurement with mass flow meter enters crude filter, remove bigger mechanical impurities in the crude oil.After the filtered oil and deodorizing oil are fully exchanged in the plate heat exchanger, heated by crude oil heater and mixed with phosphoric acid whose concentration is 85% in oil acid mixer, the addition quantity of phosphoric acid is added at a certain quantity with metering pump according to processing capacity and crude oil quality. After mixing of oil and acid, enter acidification reaction tank to reduce the content of nonhydratable phospholipid,then enter oil alkali multi-effect mixer, after good mixing of oil and lye at certain concentration pumped by metering pump, enter neutralization tank, utilize liquid level automatic control in neutralization tank to adjust the reaction time, oil after reacting in reaction tank is pumped into plate heat exchanger is heated to about 90ºC, and enters centrifuge to remove soap-stock; alkali refining adopts middle temperature reaction, high temperature separation, not only reduce saponification of neutral oil, but also improve separation effect of centrifuge and refining yield; the oil after removing soap-stock with first centrifuge enters oil water multi-effect mixer, which adopts frequency conversion control, to prevent excessive mixing intensity and oil-water emulsification.Oil after water washing enters the second centrifuge for centrifugal dehydration, control dehydration temperature at about 90ºC.Dehydrated oil is heated to about 100ºC by plate type heater, and then enters vacuum dryer for drying and dehydration, drying temperature is adjustable through automatic control, dehydrated oil enters bleaching pre-mixing tank directly, soap-stock removed from soap-stock removal centrifuge is pumped into outdoor soap-stock temporary storage tank by soap-stock pump.Water separated by water washing centrifuge enters combined water separation tank, separated oil is pumped into workshop crude oil tank, separated water is discharged to water seal pool through indoor trench to recycle residual oil in water.
--- Bleaching section Exchange heat between neutralized oil and deodorization oil, then heat to 105-115ºC by plate heat exchanger, enters premixing tank to mix with bleaching clay( 1-3% of oil weight),then overflow into bleaching tower(bleaching temperature and time is adjustable by automatic control),then it is pumped into two alternating horizontal filters by special oil slurry pump for filtration, filtered oil enters dewaxing section after polishing filtered. Waste bleaching clay is discharged to waste bleaching clay room.
--Dewaxing section:The natural oil is comprised of triglycerides mixture; due to different fatty acid carbon chain length, unsaturation degree, the composition and position of the double bond, and the distribution of each fatty acid in the triglyceride,there are differences in physical and chemical properties. Dewaxing is based on the difference in melting point of physical properties and its solubility, the oil is divided into solid and liquid part at a certain temperature. Dewaxing can improve oil quality, sensory, taste, etc.
--- Deodorization section Filtered bleaching oil enters deaerator tank directly to remove oxygen in the oil, deoxygenized oil exchange heat with deodorization oil, and heated by heat conduction oil heater to 250ºC,then oil goes through padding part by the methods of falling film countercurrent stripping, stripping capacity is high, splash is little, fatty acid can be removed rapidly to avoid hydrolysis happen; oil flows into board part through pipe, direct steam in board part erupt from oil with the shape of bubble, and contact oil for stripping again, reduce boiling point of odor matters through high vacuum in the board part, and through distillation of superheated steam to reach deodorization purpose, and delay for thermal bleaching. Deodorized oil is discharged from the bottom of deodorization tower, this process takes about 65~80min. Deodorization oil is drawn with shield pump through oil-oil heat exchanger, bleaching oil heat exchanger, crude oil heater respectively,and finished oil cooler to cool the oil below 40ºC,finally enters finished oil storage tank through polishing filter.
--- Vacuum auxiliary sectionDrying and bleaching vacuum system adopt condenser and water circulating vacuum pump types,circulating cooling water which is cooled by frozen water in condenser can be recycled. This system do not use steam,little power consumption, less running machines, and its convenient for maintenance. .Deodorization vacuum system adopts combined types of steam jet vacuum pump, condenser and water circulating vacuum pump, steam jet pump adopts 9bar steam, energy-saving, reduce steam consumption, cooling medium of deodorization vacuum system adopts 25ºC∽28ºC cooling water, cooling water can be recycled after cooling by cooling tower. --- Process technical feature: - The whole plant adopts waste heat utilization technology. In every section, set energy-saving heat exchanger, finished oil at high temperature to do heat exchanging with bleaching oil, dry oil and crude oil in turn from high to low according to different process temperatures, which can make maximum use of waste heat of deodorization finished oil,reduce steam consumption. All steam condensate water of heating equipment is recycled into hot water tank for reuse.
- Drying of water washing oil adopts vacuum drying technology, compare with traditional technology, not only reduce steam consumption, but also prevent oil from contacting air,reduce oil oxygenation efficiency, keep the maximum inherent nutrition value.
- When blow bleaching clay,design odor trapping device, use circulating water cooling to catch odor of blowing steam, remove odor pollution in the decolorization process, meet environmental requirement.
- Set self-spraying device in waste bleaching clay room, spray cooling water when discharging cake from filter, ensure effective cooling of bleaching clay, avoid spontaneous combustion of bleaching clay, play a role safe production.
- The crystallization tank adopts vertical structure internal stirring system,with advantages of long crystallization time, large crystal particles and good dewaxing effect.
- The entire workshop is fully automated, and all key control points such as temperature, pressure and liquid level are displayed on the computer and automatically controlled. Final Oil Quality Index after refining (Sunflower oil Chinese Standard Grade 1)
Item | Quality index |
Refined oil color(Lovibond cuvettes133.4mm) | Y15,R 1.5 |
Smell,taste | No smell,good taste |
Transparency | Clear and transparent |
Moisture and volatile matter | ≤0.05 |
Insoluble impurities (%) | ≤0.05 |
Acid value (mg KOH/g) | ≤0.2 |
peroxide value (m mol/kg) | ≤5.0 |
Smoke point(ºC) | ≥215 |
Freezing test(store for 5.5h at 0ºC) | Clear and transparent |
Residual solvent (mg/kg) | No |
Our main project scope include--10~5000TPD oilseed pretreatment project
--20~5000TPD solvent extraction project
--10~500TPD oil refining project
--10~500TPD oil fractionation project
--Protein and phospholipid project
--Grain processing projectTypical project--10~1000TPD rice bran pretreatment & expansion and rice bran oil extraction project
--10~600TPD grade 1 rice bran oil refining project
--150~1000TPD cottonseed protein dephenolization project
--10~100TPH palm oil project
--10~2000TPD corn processing project
--10~500TPD non-acid catalysis biodiesel projectLatest Technology
--Oil deodorization and vacuum energy-saving technology
--Protein concentrate extraction technology
--Miscella refining technology
--Molecular distillation technology
--Extracting sugar from broken rice technology
--Fully-continuous lignite wax extraction technology (the first production line in Asia)